brochure du chopper hopper de nov mono
brochure sur la pompe broyeur chopper hopper
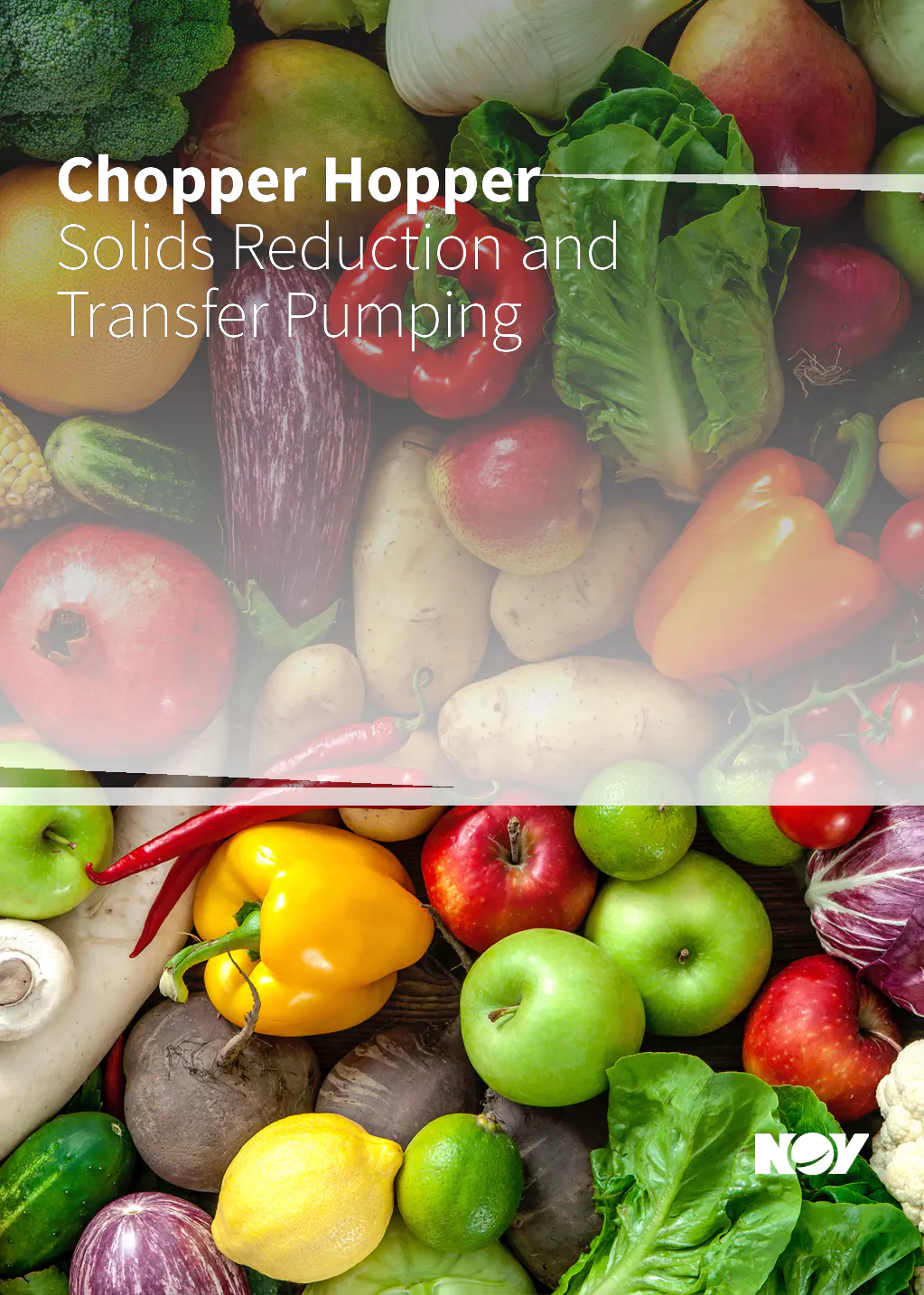
Contenu du document
Chopper Hopper
Solids Reduction and Transfer Pumping
Ensuring waste is never wasted.
The Chopper Hopper is a powerful and aggressive grinder pump that combines solids reduction and transfer pumping into one efficient unit. It homogenizes objects like whole fruits and vegetables into a pump-able puree or mash. Up to three stages of solids reduction are available for coarse, medium, and fine particle size.
Features and Benefits
- Ease of Processing: A grinding and pumping operation in a single, compact operation with fast process times due to a large surge capacity hopper and high flow rates.
- 3 Stage Solids Reduction: Available for coarse, medium, and fine particle size. Drastic size reduction occurs in the first stage where fierce cutting blades grab, tear, and shred solids, as big as whole watermelons, down to a particle size of less than 1” in a single pass. Second and third stage grinding provides the desired solid size and texture needed.
- Multiple Cutter Designs: Angled cutters for grabbing or tearing large size objects with additional cutters located in the extension tube for further solids reduction. The design allows for optional fine grind conditioning through homogenizing units.
- Materials of Construction: Available in carbon, stainless steel or specialized materials of construction.
- Gear Joint Design: The design of this progressing cavity pump allows for low friction of the gear joint design, leading to less wear and better overall performance.
- Easy Disassembly: Cutter shafts and pump internals are made to be easily disassembled, reducing downtime.
Typical Applications
- Food Processing
- Waste handling for disposal
- Rework or recovery of product
- Rendering plants
- Slaughter plants - process internal organs
- Orange peels, juicers
- Waste potatoes
- Meat Products
EZstrip™ Progressing Cavity Pump
Progressing Cavity Pump now transfers pumpable slurry onward for further processing.
Feed Hopper
Objects are dropped into the hopper and are then sent through the re-breaker.
Pre-breaker
Pre-cutters break up the solids, including organic waste such as large produce and hard materials like stones and seeds.
Screw Conveyor
Objects are fed into the conveyor and mechanically transferred into the grinder.
© 2018 National Oilwell Varco All Rights Reserved
Corporate Headquarters:
- 7909 Parkwood Circle Drive Houston, Texas 77036, USA
- 10353 Richmond Avenue, 1020 Everman Parkway Houston, Texas 77042, USA
nov.com