Document
Sludge Dewatering Technology from Bucher Unipektin AG
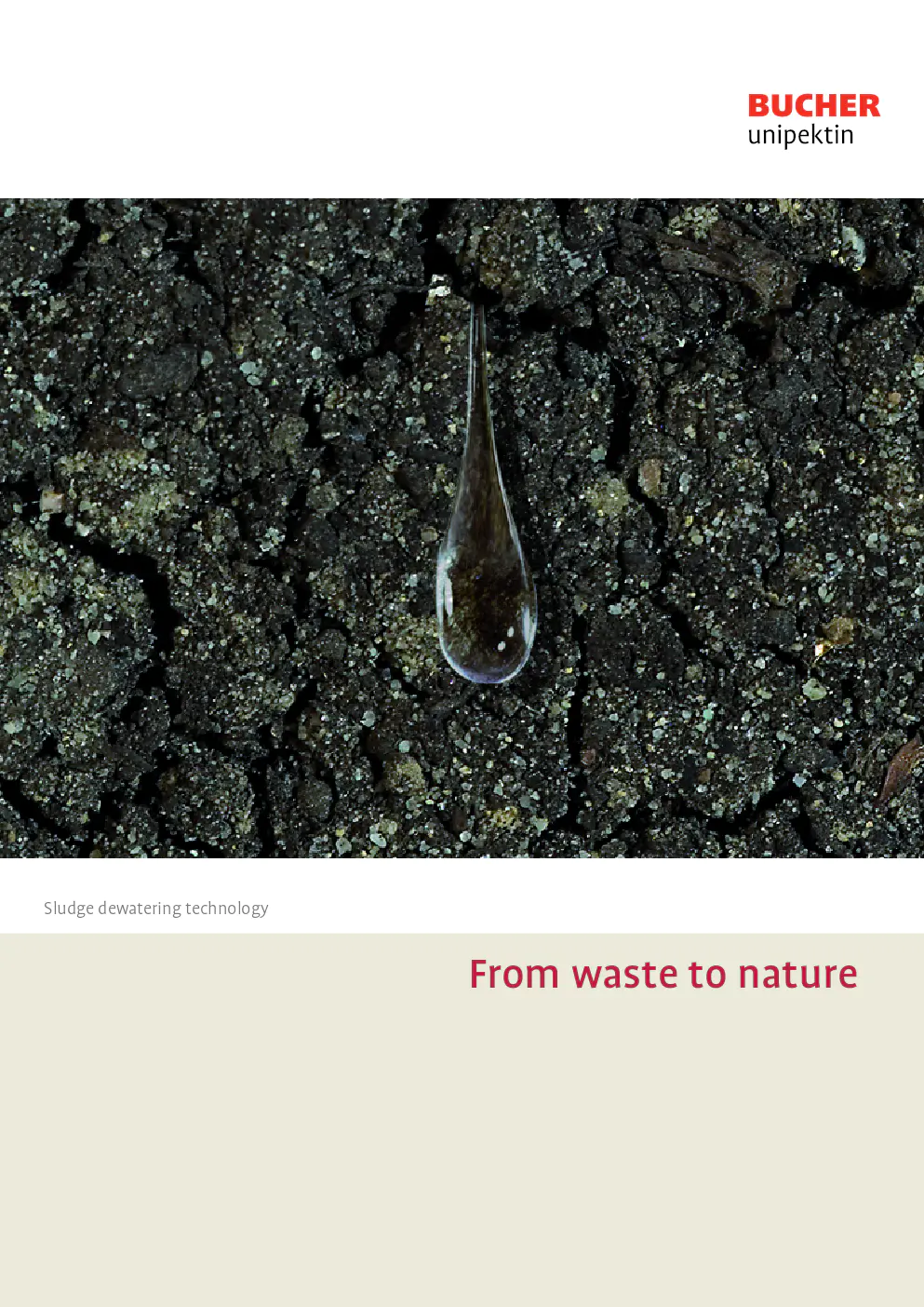
Contenu du document
From waste to nature
Sludge dewatering technology
Thickened SludgeCoagulantFlocculant
Milling chamber Clearing
tankPiston press
Discharged filtrate
3
Innovative dewatering technology
Bucher Unipektin is one of the world’s leading manufacturers of machines and systems for efficient
solid-liquid separation of biosolids. The patented technology of Bucher hydraulic presses has been
implemented in over 2000 instalations worldwide. The reliability of Bucher presses in demanding
applications and use has set new standards.
Bucher Unipektin team of experienced engineers and technicians works to meet the challenges of
tomorrow for the benefit of our customers and our environment. The challenging expectations of our
customers are the focus of our activities. Our employees in addition to a high level of training also
have many years of experience in solids-liquids separation. This allows us to offer our customers
exceptionally innovative solutions for dewatering.
Based on this experience and with further development of its robust press technology, Bucher Unipektin
has expanded the boundaries of what has to date been technically possible in dewatering of sludge.
Systems delivered by Bucher Unipektin are characterised by a high level of performance and long
service life with minimal maintenance. System design and construction are prepared and executed in a
constructive dialogue together with planners and clients efficiently and in a cost-saving way according
to specific needs.
The pivotal point of sludge treatment in both municipal and industrial sludge is mechanical drainage.
It specifies whether or not sludge utilisation can subsequently be resource-saving, energy-efficient and
thus sustainable.
Bucher Unipektin’s HPS technology ensures energy-efficient thermal utilisation of the sludge as well
as easy handling of the filter cake in agricultural recycling processes at the highest possible degree of
mechanical dewatering.
Dewatering system Filter system
Bucher Unipektin
A complete pressing cycle consists of a filling, pressing and an automatic emptyng phase.
A complete cycle takes 70 – 120 minutes depending on the drainage characteristics of the sludge.
1 Filling
The press volume is filled up by using a pump.
2 Pressing
The press piston is moved forward reducing the press volume forcing the liquid through the drainage
elements into the filtrate collection chamber at the end of the cylinder.
3 Loosening
The press piston is pulled back. The slow rotation of the cylinder and movement of the drainage
elements allows the filter cake to fragment into pieces. The vacuum created in the cylinder causes a
back flow through the filter sleeves thus cleaning them. During the next pressing phase the filter cake
effectively assists in the filtering.
The process steps 1, 2 and 3 are repeated until a sufficient quantity of filter cake has developed in the
press space. The actual pressing phase follows by alternating process steps 2 and 3 until the desired
degree of dewatering is achieved.
The high degree of dewatering is due to the short flow path of the liquid to the filter elements through
frequent pressing and loosening.
4 Emptying
When pressing is complete the press space casing is hydraulically opened and the filter
cake is discharged by the press piston.
High performance through proven methods
1 Filling 2 Pressing 3 Loosening 4 Emptying
piston
piston
Filling
Pressing
Emptying
5 min
Filling 60 to 70 min Filling pump
operation
Pressing 60 to 70 min
Stroke
Time
Cake dryness
Cake dryness evolution
during the cycle
Pressing Filling
time
5
Operation safety through self-optimising controls
Maximum dewatering performance is achieved with self-optimising controls. The operator may select the
degree of dewatering or the pressing time.
The press is operated from a user-friendly operator interface with process visualisation. The relevant
process data is displayed.
The high level of automation combined with the self-optimising controls guarantee maximum operational
safety and performance with a minimum of operator input.
Cylindrical drum Press residueHydraulic aggregate
Bucher Unipektin
Sludge dewatering is currently facing several challenges which are already being covered by the Bucher
press:
Increase of energy efficiency
The newly developed hydraulics could reduce the HPS energy requirement by 20%. Therefore, depending
on the type of sludge, the actual energy requirement for dewatering with HPS technology lies in a range
of 20 to 50 kWh/t dry residue.
Low backflow load of the filtrate
Due to the filtration process used in connection with sludge conditioning, the backflow load of the
filtrate by solids will be reduced to a minimum. This significantly simplifies a filtrate aftertreatment.
This is especially true for the recovery of primary resources (P, N, etc.).
Maximum drainage
Comparing the technologies, it can be seen that the Bucher press achieves significantly higher dry
substances than conventional processes. The better the drainability of a sludge, the greater the
difference to other processes.
Thermal utilisation of dewatered sludges
The HPS technology can achieve autothermal levels for almost all types of sludge. This allows direct
thermal utilisation of HPS dewatered sludges without the implementation of a cost and energy intensive
thermal pretreatment. As a result, the best possible energy balance in the sludge treatment can be
achieved.
Minimal disposal costs by maximum drainage
Drainage Core
Filtrate
Filtercake
Filter Cover
Drainage core HPS filtering system
Press HPS 6007
Quality and service
Quality
Unipektin processes all orders with the same care, whether for individual plant components, complete
processing lines or spare parts. Bucher Unipektin systems stand out for their high availability and long
service life with minimal maintenance.
We are ISO 9001:2015 certified.
Innovation
With the development of the HP system, Bucher Unipektin has succeeded in revolutionizing the press
technology in a sustainable way. Bucher Unipektin has a whole team of experienced development
engineers working on the press technology of tomorrow – for the benefit of our customers!
The requirements and wishes of our Customers are always the focus of our activities.
Worldwide service
In order to guarantee optimally functioning systems to our customers, our commissioning engineers
will intensively train and instruct your operating personnel on site.
The support team in our customer service and after-sales department consists of experienced
professionals. Our central spare parts warehouse guarantees a long-term availability of spare parts
as well as fast and reliable delivery worldwide.
For a personal consultation of our service and service packages, please contact our customer service.
Further information can be found on our website.
Panel displaySpare partsService
7
Bucher Unipektin
BRO-UT-EN-20180&?TFBu
cher Un ipektin AG
s?8v
M urzlenstrasse 80
C H-816 6 Niederwen inge n s?8v
P hone s?8v +41 44 85 7 23 00 s?8v
F ax#"V?)+41 44 857 23 41 s?8v
i nfo @bucher unipektin.com Bu
cher Un ipektin AG
s?8v
1?0F 1i ?&"0f?2?gq??"?B&s @0cP? 3?4!s#Va1? ?"?Bvyr@'? ?q!45?!4?Y2?gq?GGAU2?gq?BU?29db` s?8v
M oosmühlestr asse 8
C H-900 0 St. Gal len
Pho ne s?8v +41 44 85 7 29 00
F ax#"V?)+41 44 857 29 91
info.ccf
@
bucherunipektin.com
B
ucher Un ipektin AG
s?8v
O ddzial w Polsce
Al . Niepodlegtosci 107/109 -39 s?8v
P L-02-626 Wa rszawa
P hone s?8v +48 22 84 4 85 29
F ax#"V?)+48 22 844 85 29 s?8v
i nfo @bucher unipektin.com B
ucher Un ipektin AG
s?8v
ApIW) 7?03FU`?AR#)$R?
??B? AU1!45?23`q? B?Pfft"$Xe!Xh1xdW%1B?PfffC@%`?%`?!45?2&?@?T@#F1) %cY`
P?dV@ !45?21v4DH 03FU`XFr)8P4xwCY&?3dTU??"?BXFr)2?gq??c?1
7A8w 8I??x BwW! 6x7B 03FU`XFr)0BGqYbi
&dD?c @p?#G%??"?B1YxC? HX5XfXqPPsa 4y H3R!p9)
t 0BG2?!9#"V?)?t&q0q?B#?7RB PPsa 4y H3R0`?@
i nfo @bucher unipektin.com
www.bucherunipektin.com
Switzerland China
New Zealand
Russia
Bucher Unipektin AG worldwide Be
ijing Bucher Unipektin
E quipme nt Co. Ltd.
R oom 1909 Twin Towers s?8v
U pper East Side, No.2 s?8v
Do ngs ihuan Beilu s?8v
C haoyan g Distr ict
C N-Beijing 100 016
P hone s?8v +86 10 59 78 26 08 s?8v
F ax#"V?)+86 10 597 8 26 09 s?8v
in fo@ bucherun ipektin.com Bucher Alimentech Ltd. s?8v
Le
vel 1, 10 Arthu r Brown Place
s?8v
M t. Well ingto n
P O Box 142 58 Pan mure
N Z-1060 Aucklan d
P hone s?8v +64 9 573 1333
F ax#"V?)+64 9 573 133 4 s?8v
in fo@ bucherun ipektin.com
Locations Agencies
Entreprises concernées :
Date d'upload du document :
mardi 26 mai 2020