profil d'entreprise future pipe industries
profil de l'entreprise future pipe industries
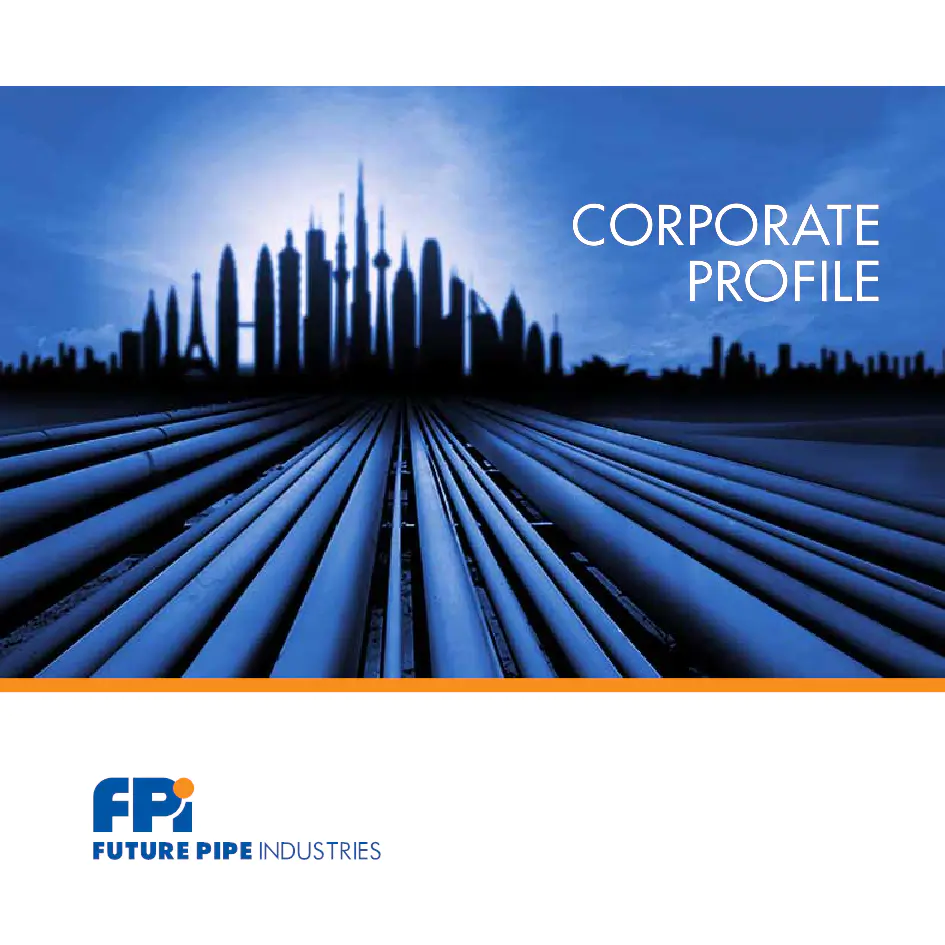
Contenu du document
Corporate Profile
To deliver Water and Energy to the world, in the most efficient way
- Employees: 3300
- Customers: 400
- Factories: 13
- Build-up Area: 681,000 sqm
- Sales offices: 20
- In Countries: 50
- Production lines: 53
- Output Capacity: 4,800 km/year
Our History
Future Pipe Industries (FPI) is the worldwide leader in engineered, performance-based fiberglass pipes and fittings. With a comprehensive product portfolio of fiberglass pipe systems, FPI has a solid reputation for designing, manufacturing, and installing bespoke pipe solutions for leading companies in infrastructure, oil and gas, industrial, water, and marine fields.
Established in Dubai, UAE in 1984, FPI aimed to be a leading manufacturer and technology developer of fiberglass pipe systems. From the mid-nineties, FPI embarked on a global expansion by developing its own pipe system technology and expanding production capacity. Recently, FPI acquired Specialty Plastics Inc. and Protesa, marking continued global growth.
Our Mission
To elevate fiberglass to a material of choice and position FPI as the recognized market leader by:
- Working alongside our customers
- Differentiating our offering through evolving into a focused solution provider
- Delivering innovative pipe systems and bespoke services
What We Do
FPI offers the largest and most versatile large diameter fiberglass pipe product range. Managing a unique global delivery model, FPI aims to deliver water and energy efficiently. FPI also emphasizes quality, maintaining certifications by international bodies and committing to high safety and environmental standards.
Our Products
FPI provides a range of products, including glass reinforced epoxy and polyester pipes, with capabilities in high pressure and offshore applications, supporting diverse industrial needs.
Manufacturing
FPI employs advanced manufacturing processes such as helical filament winding and continuous filament winding to produce high-quality products.
R&D and Testing
Future Pipe Industries offers advanced R&D and testing services to ensure product excellence and adherence to international standards.
Site Services
FPI offers comprehensive site services, including installation and training, ensuring projects meet all necessary regulations and quality standards.
Our Sectors
FPI provides complete pipe systems solutions across three sectors: Water, Oil & Gas, and Industrial.
Engineering Leadership
Through ENOIA, FPI offers world-class consulting and engineering services.
Quality Excellence
FPI's commitment to excellence is evidenced by its extensive product portfolio and accreditations.
Our Commitment
FPI aims to enhance its market share, strategically position fiberglass, and maintain its reputation through research and development.
All of Future Pipe Industries' factories are ISO certified.
Visit www.futurepipe.com