fiche technique des débitmètres à ultrasons ES-FLOW
fiche technique sur les débitmètres à ultrasons ES-FLOW pour liquides à faible débit
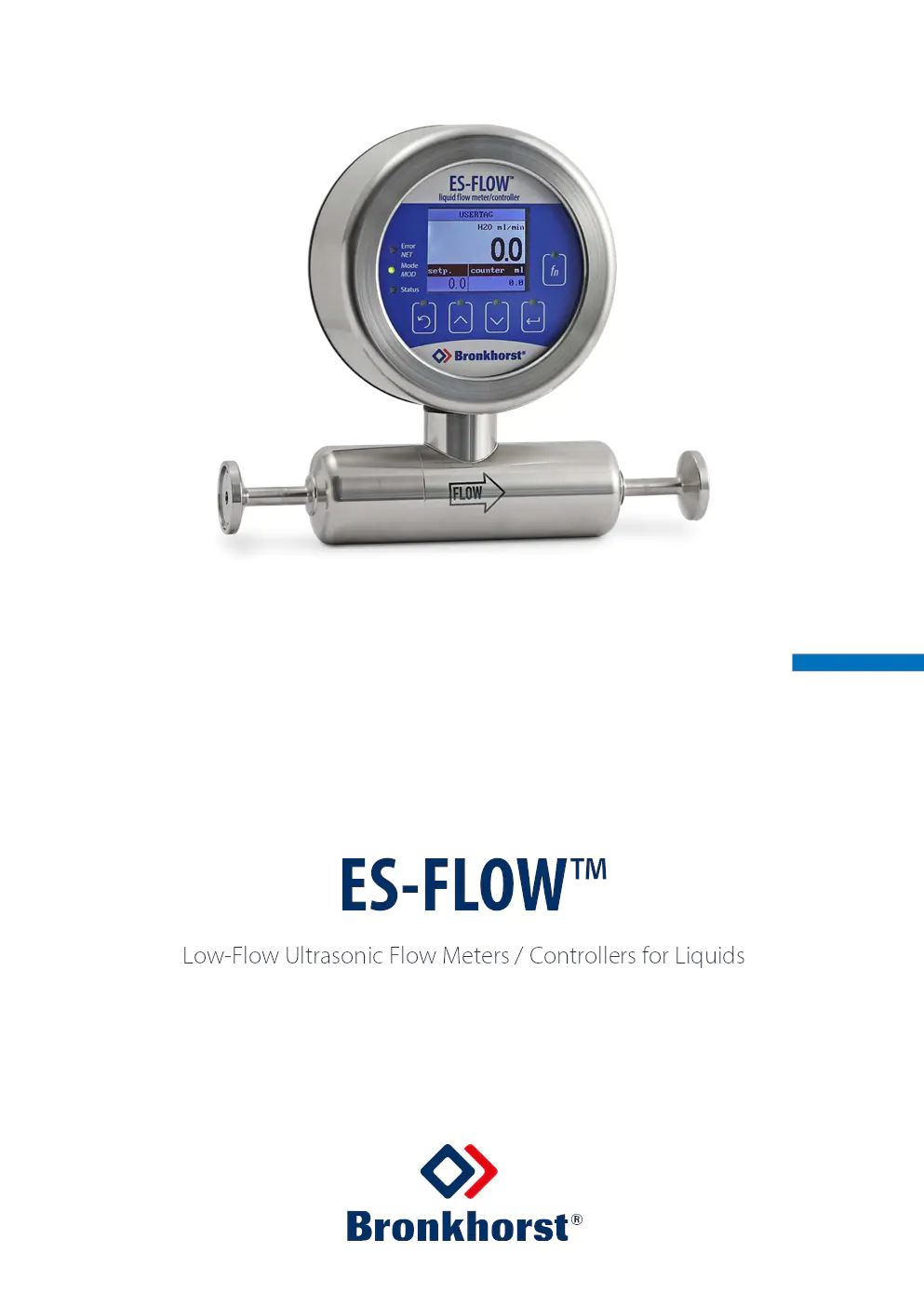
Contenu du document
ES-FLOW™
Low-Flow Ultrasonic Flow Meters / Controllers for Liquids
Ultrasonic flow meter for low flow rates
The innovative ES-FLOW™ Ultrasonic Liquid Flow Meter/Controller is designed for measuring volume flow ranges between 4 and 2-1500 ml/min with high precision, high linearity and low pressure drop using Ultrasonic Wave Technology in a small bore tube. Liquids can be measured independent of fluid density, temperature and viscosity. Therefore, recalibration per fluid is unnecessary as the instrument is able to detect the actual speed of sound of the measured liquid. With these features the ES-FLOW™ has many similarities with our Coriolis technology based instruments, which are very beneficial compared to Magnetic flow meters or other types of flow meters. With the ES-FLOW™ non-conductive liquids like hydrocarbons, demineralized water and oil-based additives can be measured.
Improved ES-FLOW™ Mk II
The know-how and experience gained in our specialized domain of developing and manufacturing flow meters have been used to improve the overall performance, hygienic design and accuracy of our ultrasonic flow measurement technology. The new and improved sensor technology meets the highest hygienic standards and is almost twice as accurate at the lower range, as the reading accuracy and the zero stability have been greatly improved. The ES-FLOW™ is available in two versions. The ES-103I is suitable for hygienic purposes, whereas the ES-113I can cover all other areas. The differences lie in certifications and the available process connections. The sensor technology and performance are similar.
Designed and authorized for hygienic applications
The ES-103I Mk II is designed for applications with the highest hygienic demands. This is achieved by using stainless steel materials and a straight sensor tube design. The acoustic actuators are positioned at the outer surface, meaning no obstacles or other kind of materials are within the flow path of the sensor. The instrument is self-draining, easy to clean and contains zero dead volume. The exterior design is rated to IP66 as well as IP67.
- 3-A authorized
- EC 1935-2004
- Stainless steel wetted parts, no elastomers
- CIP/SIP compatible
- Surface quality wetted parts Ra
Ultrasonic Wave Technology
The operation of Bronkhorst® ES-FLOW™ flow meters is based on the propagation of ultrasound waves inside a very small, straight sensor tube, without obstructions or dead spaces. At the outer surface of the sensor tube multiple transducer discs are located which create ultrasonic sound waves by radial oscillation. Every transducer can send and receive, therefore all up- and down-stream combinations are recorded and processed. By accurately measuring the time difference between the recordings (nanosecond range) the flow velocity and speed of sound are calculated. Knowing these parameters and the exact tube cross-section, the ES-FLOW™ is able to measure liquid volume flows in the range of 4 up to 2-1500 ml/min. The distinctive character of this flow meter is that it’s capable to measure the actual speed of sound, meaning that the technology is liquid independent and calibration per fluid is not necessary.
Benefits of the ES-FLOW™
- Direct volume flow measurement, independent of fluid properties
- Lowest flow ranges on the market (ultrasonic principle): 2…1500 ml/min on-site re-rangeable
- Hygienic design, IP67 rating, CIP/SIP cleanable, self-drainable
- Very small internal volume (ca. 2 ml), no dead volumes
- Compact and easy to install