Document
CLEACOM_072014_eng.pdf
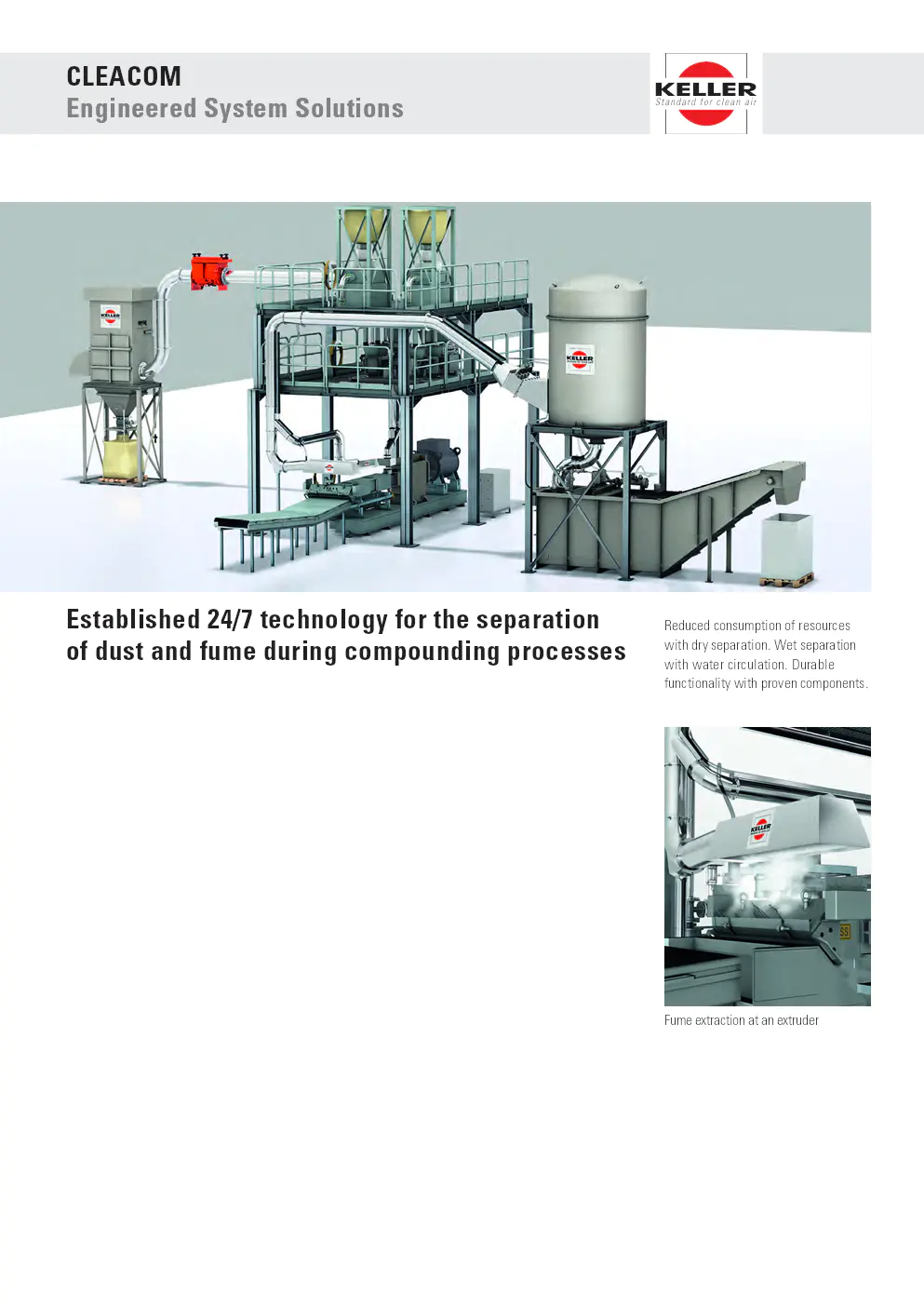
Contenu du document
Established 24/7 technology for the separation
of dust and fume during compounding processes
Fume extraction at an extruder
Reduced consumption of resources
with dry separation. Wet separation
with water circulation. Durable
functionality with proven components.
CLEACOM
Engineered System Solutions
2
Keller Lufttechnik has considerable
experience with the treatment of dust,
fume, gaseous and adhesive aerosols
released during compounding and ex-
trusion processes. Utilizing established
technology, emissions are extracted
properly at the source and separated in
centralized or decentralized systems. Fillers, fibers, additives, pigments and
liquids (curing agents and lubricants)
do affect emissions in a variety of
ways. Since dusts can be flammable or
explosive, Keller offers comprehensive
advice and performs appropriate analy-
ses.
Efficient and reliable 24/7 separation of emissions
All-in-one solution
for maximum
efficiency during
compounding and
extrusion processes.
Keller Lufttechnik
analyses specific
processes and
delivers turn-key
all-in-one solutions
Extensive demands are placed upon
all components to ensure maximum
productivity during the refinement and
packaging of plastics employing plas-
tics granulation. Besides process technology, a major
consideration is the collection of dust
and fumes and controlling the air quality
inside the workplace.
3
... with proficiency and expertise
Aerosols and fumes are released dur-
ing extrusion processes. They are
captured with collection hoods, rinsed
with water and fed to a wet scrubber. The wet scrubber utilizes water as fil-
tration medium – with the advantage
of a maximum operating safety despite
adhesive emissions.Dusts from the treatment section (mix-
ing, weighing, feeding) are added to
a dry separator. Pollution and surface
dust is extracted manually with an-
other vacuum creating dry system. As
a general rule, other designs and con-
figurations are possible, upon request. Three extraction
systems combined
can fulfill all the
extraction require-
ments
The modular design of Keller com-
ponents provides a variety of solu-
tions. Compact single systems can be
equipped with the same high-efficiency
technology as systems with several
compounding lines. Harmful substances such as sedimented
sludge can often be collected. (See page
11)
Keller systems are suitable for initial
start-up, renovations, or retrofitting of
existing systems. Perfect for start-up,
renovation or
retrofitting
Example:
The delivery and supply of raw materi-
als is managed differently, depending
on demand and physical location. The
prototype illustrated in this brochure
assumes supplying with Big Bags or
sacks.
The dosing stage is located above the
extruders and the raw materials are
dispensed above the dosing stage.
4
Reliable separation of emissions and fumes at the extruder
The degassing of volatile components
occurs in the degassing zone at the
extruder head, during fabrication of
plastic compounds such as molten
polymer, vinyl acetate, POM, PC, and
ABS, thereby removing fumes, airborne
particulate, and adhesive aerosols.
Without suitable extraction methods,
these emissions would otherwise be
directly discharged into the environ-
ment.
This is the primary reason for taking
into consideration the presence of
hazardous agents and the air quality
standards within the workplace. Degassing during
extrusion processes
Fumes from degassing at the extruder head and at the preliminary degassi\
ng step can be
collected by extraction hoods and directed to the separation
Requirements for the air quality at
workplaces and the reduction of air -
borne pollutants are described in VDI
guideline 2262-3. Workplace limit values are outlined in
the Technical Rules for Hazard Sub-
stances (TRGS 900) of the Federal Insti-
tute for Occupational Safety and Health. Air decontamination
is the basis for
specific requirements
Airborne pollutants
must be extracted
reliably
Airborne emissions from extruders
must be reliably extracted. A key pre-
requisite for optimal fume collection is
installing the correct extraction hood.
Since extruder installations are cus-
tomer-specific, Keller offers a wide
range of movable or stationary extrac-
tion hoods.
Additional exhaust
air extraction during
vacuum degassing
Connection of the fume extraction to the
vacuum degassing station Collection hood
Pre-spraying
Return pipe
Folding collection hood (option) for an easy
cleaning and preliminary spraying Movable collection hood
Extraction through hinged support arms
5
Pre-spraying for wet separation
There exists a risk of deposit build-up
from adhesive aerosols. System dam-
age or breakdown could be the end
result with the potential of igniting
fires inside the ductwork. Adhesive aerosols
have a tendency to
accumulate in the
dirty air ducts …
Airborne substances
are flushed out with
water … but atomizing with
water at the collection
point alters this
effectively
Pre-spraying occurs behind the collec-
tion hoods (condensation and pre-sep-
aration stages) which are connected to
the central water supply. The prelimi-
nary spraying creates a dense and fine
water droplet curtain which saturates
the air moisture and cools down the
extracted fumes. This adiabatic cooling leads to conden-
sation of gaseous components such as
high flashpoint solvents following the
preliminary spraying in the extraction
pipes.
Pictured above:
Water hoses for the preliminary spraying
lie in the channels on the extraction pipes.
Each spraying point is operated separately
from the water treatment station.
Airborne substances are flushed out
the dirty air duct and collected in a
container together with excess water
from the preliminary spraying.
Water from the preliminary spraying is
discharged by a separate channel for
additional water treatment.
The majority of the
extracted airborne
substances flow into
the wet separator
with the water
droplets The dirty air ducts are free of deposit
build-up to a great extent, which main-
tains consistent preliminary separation
efficiency for longer periods of time.
The technology of the VDN-TA wet
separator is based on the Venturi principle
6
Separation of water combined with air and emissions
VDN-TA wet separator VDN-TA wet separator consists of a
combination of various components
and functions. It offers a dual stage
separation system with preliminary
spraying and main spraying.
Main spraying
The separated air is accelerated by
the Venturi nozzle. A water curtain
is formed directly behind the nozzle
which moistens the solid and liquid
aerosols.
Separation of water droplets and air
The water/air mixture which radi-
ally flows into the droplet separator is
separated by the cyclone principle. The
water which is combined with airborne
particulate flows out into a water
treatment tank.
Fan
Radial fans are used for wet separation
processes.
7
Water treatment for recycling
Because of the intensive use of water,
the spraying system is based on a water
circuit. Solely the volume of water from
wetting the suction air and the sludge discharge has to be refilled. The chemi-
cal consistence of the extrusion emis-
sion can require an additive feeding to
the water circuit. Water circuit
Central water treatment
The contaminated water is discharged
into the water treatment tank via the
pipe connection.
Additional waste water is pumped into
the same tank. Sludge is formed from
sediments and surface contaminants.
Adequately treated water in this circu-
lating system can be re-used for spray-
ing purposes.The water which is cleaned sufficiently
by this separation in the water circuit
can be reused for the spraying.
A skimmer is used for lightweight fluids
such as oil for surface separation. Water treatment
... with integrated
de-sludger
The de-sludger is adapted to the specific
flow conditions of waste water, circu-
lating system water and replacement
water.
8
Extraction of dusts from the treatment
De-dusting bulk mate-
rial upon refilling
storage containersThe compounding system is re-supplied
with bulk material stored in Big Bags.
Airborne particulate created inside a
dust-proof system while re-supplying
bulk material is separated and ex-
tracted.
Some supplies can be replenished
though a flap. This also activates the
extraction system.
Treatment platform with raw material added by Big Bags or sacks in the im\
age above,
below is the dosing stage.
Dust separation with collection hoods at the weighing scales above hoppe\
rs.
Dust separation with collection hoods at the extruder’s feed throats
Separation of dusts
from displacement air
Dust clouds may rise when pour
-
ing bulk materials onto the weighing
scales. Special collection hoods sepa-
rate dispersed residual dust at the end
of the supply piping.
The material is conveyed through pipe-
lines into the extruder. At the terminal
end, replacement air and residual dust
are extracted by optimized collection
hoods.
Closed extraction to separate the bulk
material during the feeding of raw material
(Big Bags or sacks)
9
… dry extraction and separation
VARIO dry separators in various sizes
are used for the extraction of dry dusts.
Y-filters efficiently separate dust par-
ticles. With the use of efficient filters, the
clean air can be re-directed into the
manufacturing area.
The filter cleaning is effected by com-
pressed air pulses during operation. VARIO dry separator
VARIO dry separator in standard design
VARIO dry separator (ATEX compliant)
equipped with explosion pressure surge
resistant housing design and suitable
discharge lock. Additional flameless
pressure relief is provided by a Q-Box
or by a ProFlap back pressure flap.
An explosive environment can be cre-
ated depending on the character and
composition of the dusts. For additional information please visit
our homepage www.exschutz.net Caution!
Dust explosion risk
If explosion protection measures ac-
cording to ATEX 95/137 are required,
relevant regulations are mandatory.
Q-Box
The VARIO dry separator is equipped
with a Q-Box for interior flameless
pressure relief. Burst panels can be
installed on an exterior wall for indoor
installations, or on the exterior of the VARIO housing for outdoor installa-
tions.
ProFlap back pressure flap
A ProFlap back pressure flap provides
effective additional explosion protec-
tion. The dirty air duct is closed auto-
matically in the event of an explosion
shock wave.
Discharge lock
As another measure for explosion pro-
tection, VARIO disposes of a flame and
pressure proof discharge unit. Constructive explo-
sion protection
according to ATEX
guidelines
10
For manual dust extraction
Central vacuum
suction unitIn addition to the previously described
extraction systems, it would be wise
to utilize a highly efficient centralized
system even for surface cleaning. Keller
Lufttechnik offers a variety of vacuum
suction systems.
The vacuum suction system consists
of:
R?#H
Suction nozzles
R?#H
Channels with quick-connect couplings
R?#H
Piping
R?#H
Dedusting unit with round filter and
collection tank
R?#H
V
acuum unit (adequate)
The dust attains the filter material as
dust-air mixture with relatively fine
particles through a pre-separation for
coarse dirt particles. Dust is further
filtered from the air flow and collected
in containers or discharged by appro-
priate discharge systems.
Several multiple stage fans, side chan-
nel blowers or rotary blowers are used
to create a vacuum.
Many dusts are combustible and explo-
sive. For information please see page 9.
Detailed information about ATEX, fire
and explosion protection can be found
on our homepage www.exschutz.net
Components
Separation of dirt and
dust
Vacuum creation
Fire or explosion risk?
Vacuum suction
system for operation
with external vacuum pump
Suction hose with changeable suction nozzles.
Several suction stations can be used simultaneously.
11
Each solution can be customized
Wet and dry separation system, all components on the same level
System installation on three levels
Dry separation for dosing platform and extruderWet separation extruder
Water discharge (preliminary spraying)
Waste water recirculation
Dust extraction from treatment
Discharge pipe for central
vacuum system
CLEACOM
Your benefit from our experience
© Keller Lufttechnik - all rights reserved. Subject to modifications.\
06/2014
Wet scrubber with water treatment tank Dry separatorCentral vacuum suction system
Collection of gases and aerosols at the extruder
CLEACOM
project consultation
We are pleased to offer you a consulta-
tion without obligation by recommending
individualized solutions for retrofitting,
renovation or installing new systems.
Do not hesitate to contact us in the explo-
ration period of your project.
We are especially qualified to provide
you with specific information on fire and
explosion protection.
Please visit our new homepage
www.exschutz.net
Entreprises concernées :
Produits concernés :
Date d'upload du document :
mercredi 25 septembre 2019