documentation sur les systèmes de surveillance des émissions continues et contrôle des processus pour les usines de valorisation énergétique
guide sur les systèmes Opsis pour le contrôle des émissions et des processus dans les incinérateurs de déchets
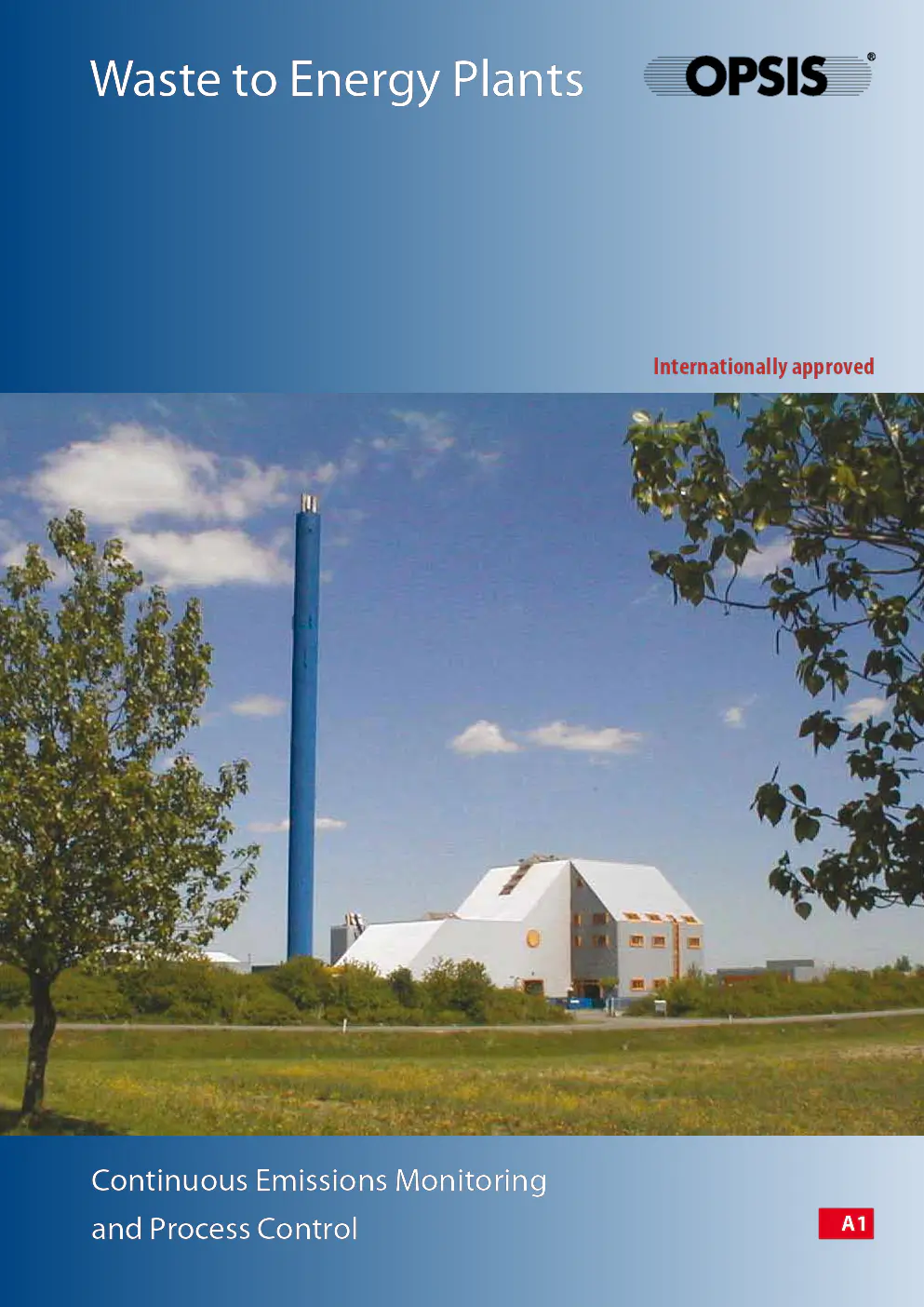
Contenu du document
Les Continuous Emissions Monitoring and Process Control in Waste to Energy Plants permettent aux autorités locales d'incinérer des déchets domestiques et autres types de déchets, incluant généralement des plastiques, des batteries et divers composés inconnus. Ces éléments peuvent produire des émissions acides et toxiques. Par conséquent, des systèmes de nettoyage des gaz de combustion efficaces sont nécessaires pour empêcher leur libération dans l'environnement.
Le système Opsis
Les systèmes de surveillance des émissions Opsis sont conçus pour ces applications. Ils reposent sur des technologies de surveillance optique, DOAS FTIR et diode laser réglable. Cette technique est la plus adaptée à l'application actuelle. En utilisant DOAS FTIR, on obtient un système de surveillance à chemin ouvert, sans contact, non affecté par les gaz, températures et matières particulaires typiques des conditions de cheminée. La capacité de surveiller en continu une gamme de composés spécifiés par l'utilisateur en temps réel avec un seul système offre la réponse rapide nécessaire au contrôle des processus.
Par exemple, avec les processus SCR et SNCR, Opsis surveille en continu le monoxyde d'azote (NO), le dioxyde d'azote (NO?) et l'ammoniac (NH?) dans les gaz propres et bruts et contrôle le dosage de NH?/urée. Un autre exemple est la surveillance du dioxyde de soufre (SO?), du chlorure d'hydrogène (HCl), du mercure (Hg) et du fluorure d'hydrogène (HF) avant et après les épurateurs utilisés pour contrôler le dosage de la chaux. Un système Opsis unique peut gérer plusieurs chemins de surveillance, rendant la surveillance avant-après avec un système unique très rentable.
Opsis peut aussi être spécifié pour surveiller le dioxyde de carbone (CO?) et la vapeur d'eau (H?O), où ces données sont souvent requises dans le cadre d'un processus de contrôle des émissions. Le laser diode LD500 peut surveiller l'oxygène (O?) et la température, tout en contrôlant les niveaux explosifs de CO pour le contrôle des filtres. Opsis offre aussi des systèmes extractifs dilués et chauffés ainsi qu'un moniteur portatif de mercure pour détecter Hg total et Hg atomique.
La technique Opsis
Un système Opsis inclut un ou plusieurs trajets lumineux traversant des cheminées ou conduits. Dans chaque trajet, la lumière est projetée d'un émetteur à un récepteur, puis transmise à l'analyseur Opsis via un câble à fibre optique. En utilisant la loi de Beer-Lambert, l'analyseur détecte et mesure les composés spécifiés dans le logiciel du système et enregistre les données sur un disque dur, soit sur un PC local ou distant. Ce système permet aussi l'intégration avec d'autres systèmes de l'usine via des communications série, faisant d'Opsis un système de contrôle des processus.
Tests et approbations
Le système Opsis a été testé et approuvé par de nombreux instituts et autorités reconnus internationalement. Il répond à la directive européenne sur les déchets et est approuvé par le TÜV allemand et le MCERTS britannique. Des détails complets sont disponibles sur demande.
Pourquoi choisir Opsis ?
- Surveillance haute performance à travers la cheminée
- Système multi-gaz et multi-chemin
- Combine les avantages des technologies DOAS FTIR et TDL
- Pas de prélèvement requis, système de mesure sans contact
- Opère dans des environnements difficiles
- Nécessite peu de maintenance
- Basse consommation d'énergie
- Approuvé internationalement
- Des centaines de systèmes installés dans le monde entier
- Réseau de service expérimenté et qualifié
Coordonnées :
OPSIS AB
Box 244
SE-244 02 Furulund, Sweden
Téléphone international : +46 46 72 25 00
Télécopie internationale : +46 46 72 25 01
Email : info@opsis.se
URL : http://www.opsis.se